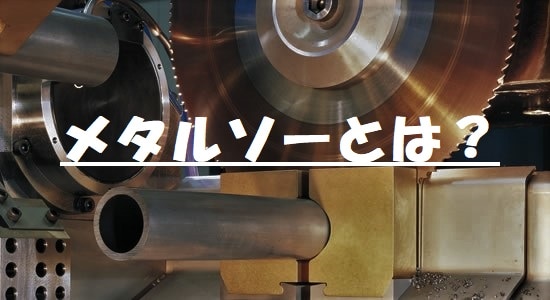
Was ist eine Metallsäge? Erklärung zu Materialien und Klingentypen!
Inhaltsverzeichnis [versteckt]
- 1.Wasist eine Metallsäge?
- 2.Überdas Material der Metallsäge
- 3. Informationenzum Schneiden mit einer Metallsäge
- 4. Informationen zumMetallsägeblatttyp
- 4.1.高低刃(HZ・C)
- 4.2.交互刃(チドリ・BW・面取り)
- 4.3.溝刃(ノッチ・CB・BN)
- 5.Zur Tonhöhenauswahl
- 6.Über SZ (Schnitttiefe pro Zahn)
- 7.Über den Winkel der Metallsäge
- 8. Überdie Beschichtung
- 8.1.鋸刃の耐摩耗性の向上
- 8.2.生産性の向上
- 8.3.費用と作業性の改善
Was ist eine Metallsäge?
メタルソーとは、切断するために金属で作られた円盤状の鋸です。
下記のように各部位に関して名称があります。
①ボア
切断機械と接続する穴部。径(大きさ)は機械メーカー、機種により異なります。
ボア径は、32h(ボア径32mm)、50 h(ボア径50mm)と表されます。
②ピンホール
切断機械と接続する際の補助となる穴部。
ピンホールの数、径(大きさ)は機械メーカー、機種により異なります。
③ハブ
切断機械と接続する際の、機械と接触する中心端面。
④有効径
切断できる範囲です。研磨するたびに、減少します。
⑤ピッチ
鋸刃の山と山の間の長さを表します。上記図の場合、ピッチ5mm P5と表します。
メタルソーを型式を表現する際は、
315Φ(外径)× 2.5t(厚さ)× 32h(ボア径)× P5(もしくは刃数)+ 刃型
などと表し、それぞれに意味があります。
>>Laden Sie den Metallsägenkatalog von Daido Kogyo herunter
Über das Material der Metallsäge
メタルソーと呼ばれる高速度鋼(こうそくどこう、high-speed steel)は工具鋼における高温化での耐軟化性の低さを補い、より高速での金属材料の切削を可能にする工具の材料とするべく開発された鋼です。高速度工具鋼(high-speed tool steel)とも呼ばれます。
「ハイス」の呼称は、「ハイスピード・スチール」が縮まったもので、また、HSSと略記される高速度鋼は、高温化での硬さや耐軟化性を高めるべく、鋼にクロム、タングステン、モリブデン、バナジウムといった金属成分を多量に添加したもので焼入れ等の熱処理を施した後、研磨により成形して使用されています。
Im Vergleich zu Hartmetall weist es eine geringere Verschleißfestigkeit auf, weist jedoch eine höhere Zähigkeit auf und kann mit höheren Geschwindigkeiten geschnitten werden. Heutzutage wird Pulvermetallurgie eingesetzt, um die Struktur zu verfeinern und noch höhere Legierungen herzustellen.
「焼結高速度(工具)鋼」(粉末ハイス)や、物理気相蒸着(PVD)法による表面への窒化チタン(TiN)等の高耐摩耗性被膜の形成が盛んに行われており、これらを含めて超硬合金では靭性の不足する領域での金属加工に用いられる工具、主にはドリルやエンドミル、金属用鋸刃の材料として使われています。
また、コバルトを添加した高速度鋼はとくに「コバルト・ハイス」と呼ばれ、より焼きもどし抵抗性や高温硬さが高く、これは加工時により高温に曝されるステンレス鋼の穴あけなどに使用されます。
Die japanischen Industrienormen (JIS) spezifizieren 13 Arten von Schnellarbeitsstahl als „JIS G4403“. Unter diesen ist Schnellarbeitsstahl durch das Symbol „SKH“ vor der Nummer gekennzeichnet, das für Stahl, Kougu (Werkzeug) und Hochgeschwindigkeit steht.
Auszug aus Wikipedia
Denken Sie daran, dass die Materialien für Metallsägen HSS (Schnellarbeitsstahl) und Kobalt-Schnellarbeitsstahl sind. In anderen Ländern heißt es M2 M35.
Über Metallsägenschneiden
Das folgende Diagramm zeigt, wie die Schneide einer Metallsäge in das Material eindringt.
*Auszug aus Kinkelder-Materialien
Wie Sie dieser Abbildung entnehmen können, schneidet sich die Schneide der Metallsäge in das Material ein (Schneiden).
Beim Schneiden von Metallsägen entstehen Späne und durch Reibung entsteht Wärme.
*Der oben beschriebene Vorgang führt zu Verschleiß am Metallsägeblatt.
>>Laden Sie den Metallsägenkatalog von Daido Kogyo herunter
Über Metallsägeblatttypen
Wir stellen drei typische Blatttypen von Metallsägen vor.
高低刃(HZ・C)
Es gilt als der grundlegende Sägeblatttyp für Metallsägen.
被切断材:ムク材や厚肉材向け
切削抵抗:小(2刃で切粉3分割)
面粗度:粗い ピッチ:4以上
備考:難削材に対応
交互刃(チドリ・BW・面取り)
薄肉パイプ等はこちらが基本となります。
Zu schneidendes Material: Für dünnwandige Rohrmaterialien
Schnittfestigkeit: mittel (2/3 des Sägeblattes)
Oberflächenrauheit: Fine Pitch: 3-4
Hinweis: Für langsame/manuelle Maschinen
溝刃(ノッチ・CB・BN)
Die neueste Technologie ist da.
Zu schneidendes Material: Dünnwandiges Rohrmaterial usw.
Schnittwiderstand: Groß (1 Klinge teilt Späne in 2)
Oberflächenrauheit: Fine Pitch: 4-9
Hinweis: Für automatische Maschinen, hohe Rotationsgeschwindigkeit, saubere Schnittfläche
*Erforderlich Mechanische Festigkeit Beschichtung Nicht für Winkelschneiden geeignet (Winkelschneiden kann verwendet werden, wenn kein Problem besteht)
この3つの刃型が基本となっておりますが、面粗度を重視で無垢材にも溝刃等を使っている実績もあり、上記以外の刃型(例えば不等ピッチ 等)の技術探求も盛んに行われております。
*Die Einsatzgrenzen einer Metallsäge und die Kriterien zur Bestimmung, ob sie schneiden kann oder nicht, variieren je nach Benutzer. Daher ist es letztendlich wichtig, einen tatsächlichen Schneidtest durchzuführen, bevor Sie sich für den Sägeblatttyp speziell für den Benutzer entscheiden.
Wir unterstützen Sie bei der Festlegung solcher Beurteilungskriterien.
Über die Tonhöhenauswahl
※大事なことは切断長を調べること※
切断長とは、刃物が材料に対して切り込んでいくときに一番長く切削する距離をいいます。
*Aus Kinkelder-Materialien
Die obige Abbildung zeigt, wie man mit unserer Kaltenbach-Schneidemaschine ein Vierkantrohr von unten nach oben schneidet, und die Schnittlänge (die längste Schnittstrecke des Materials mit der Klinge) an der Unterseite des Vierkantrohrs. Die Abbildung zeigt die Teil wo ist länger.
この1番刃に負荷がかかる切断長を基準に刃物のピッチ(刃数)を決定する必要があります。
Warum muss die Teilung (Zähnezahl) anhand der Schnittlänge gewählt werden?
仮に切断長に対して1つの刃が下から切り込みながら押し上げられ切削する場合、材料の切粉と熱が発生します。
その材料の切粉は負荷となり、刃に対して摩耗をあたえ鋸刃の消耗を左右します。
また、切断長全体を刃物が切り込みながら進むので切粉も切断長の長さで発生することになります。
その切粉がくるくるバネのように巻かれて刃底と呼ばれる部分に巻き取られていきます。
Wie Sie vielleicht vermutet haben, führt eine kleine Steigung bei einer langen Schnittlänge zu Verstopfungen (Späne sammeln sich an der Unterseite der Klinge), und umgekehrt verbessert eine große Steigung bei einer kurzen Schnittlänge die Schneideffizienz nicht.
Abhängig vom SZ-Wert ändert sich auch die Chipmenge, dies muss also ebenfalls berücksichtigt werden. Daher ist es notwendig, je nach Schneidobjekt, Schneidmaschine und Klinge die passende Steigung auszuwählen.
Als Beispiel für unseren Pitch-Auswahlprozess, der auf dem oben Gesagten basiert, hängt beispielsweise die Belastung des Sägeblatts (bezeichnet als SZ = Schnitttiefe pro Sägeblatt) vom zu schneidenden Material und der Schneidemaschine ab Starre automatische Schneidemaschine (Umfangsgeschwindigkeit 150 m/min) mit einem High-Tech-Sägeblatt, die Schnitttiefe pro Blatt wird mit einer Belastung von SZ = 0,08 mm berechnet und die Teilung beträgt 10 für ein 50-Quadrat-2,3-t-Rohr. Das ist möglich wie folgt berechnet werden.
※計算の詳細は紙面の関係で割愛いたします。切断する機械の周速により、ピッチの考え方も変わりますので弊社にてサポート致します。
Über SZ (Schnitttiefe pro Zahn)
※使っている機械によって違います。
切り込み量とは1刃あたりにどれだけ切削をさせるかということであり、これは、刃袋(刃底)と切断長と相関関係(俗にいう目詰まり)にあるといえます。
Es hängt auch von der Steifigkeit der Schneidemaschine ab, und manuelle Maschinen sind kleiner und haben eine höhere Steifigkeit, daher ist die Einstellung höher. Darüber hinaus kann der Wert abhängig von der Klingenstärke, der Seitenform der Klinge (POWER-Form) usw. höher eingestellt werden.
基本的には摩耗の観点からも手動機等の切断時の切り上げが人力等の場合は最小で0.03mm、カルテンバッハ切断機等で比較的低速で油圧送りにて重切削をする場合は0.13mmぐらいまで設定することもあります。
また、切断する材料によりSZの考え方を変える必要もあります。
(非鉄=高く バネ鋼=低く)。
Über den Winkel der Metallsäge
*Wenn Sie versuchen, es zu ändern, könnten sich die Schnittergebnisse ändern?
γ:スクイ角度 形や材質により変化させる
鉄 基本:18度(キンケルダー社推奨) アルミ等:25度
※ 参考400~500N/m㎡ パイプ
Es ist ratsam, die Stelle zu berücksichtigen, an der die Klinge in das Material Ihrer Maschine eindringt. Jedes Unternehmen hat seine eigenen Unterschiede (Böschungswinkel, Schwung, Geradeausfahrt).
Im Allgemeinen gilt: Je härter das zu schneidende Material, desto kleiner ist der Winkel (es wird eher geschert als geschnitten) *Je näher es dem Schneiden mit einer Stichsäge kommt (erfordert Steifigkeit und Drehmoment)
α:逃げ角度 形や材質により変化させる
鉄 基本:8度(キンケルダー社推奨) アルミ:12度
※ 参考400~500N/m㎡ パイプ
Es ist ratsam, die Stelle zu berücksichtigen, an der die Klinge in das Material Ihrer Maschine eindringt. Jedes Unternehmen hat seine eigenen Unterschiede (Böschungswinkel, Schwung, Geradeausfahrt).
Generell gilt: Je härter das zu schneidende Material, desto kleiner ist der Winkel.
Aus dem oben Gesagten kann man sagen: Je schärfer die Klinge ist, desto leichter gräbt sie sich in sie ein und desto wahrscheinlicher ist es, dass sie absplittert. Je dicker die Klinge, desto stärker ist sie, aber auch schwerer zu schneiden.
>>Laden Sie den Metallsägenkatalog von Daido Kogyo herunter
コーティングについて
Heutzutage gibt es Schwarzschneider und Goldschneider, oder?
Es gibt drei Gründe, warum eine Beschichtung aufgetragen wird.
鋸刃の耐摩耗性の向上
① Verbesserte Oberflächenhärte durch Beschichtung (1.500 bis 3.500 HV)
Als Referenzhärte
HSS: 760~840HV TCT (Hartmetall-Wolframkarbid): ca. 1400HV
② Glätten Sie die Oberfläche und verringern Sie den Reibungswiderstand an der Schneidkante und der gesamten Oberfläche
③Reduziert Hitzeschäden am Sägebrett beim Schneiden
④鋸刃表面の酸化防止
生産性の向上
① Kann schnell schneiden → Kann die Umfangsgeschwindigkeit erhöhen. Kann die Schnitttiefe erhöhen
②刃先の摩耗低減によるロングライフ化
③バリの発生低減
④ Schneidöl usw. können reduziert werden
費用と作業性の改善
① Erhöhtes Produktionsvolumen pro Stunde
②Reduzierung der Belastung der Maschinen
③Reduzierung der Verbrauchsmaterialkosten durch längere Lebensdauer (insbesondere Reduzierung der Polierzeiten)
④Verbesserung der Entgratungsarbeit durch Reduzierung von Graten
⑤Reduzierung der Sägeblattwechselzeit usw.
⑥切削油を少なくできることによる消耗費軽減や作業環境の改善
コーティングの鋸刃は値段も高いですが、その分ライフが伸びれば特に再研磨するメタルソーは 研磨回数分 ✖ 伸びた本数分 の費用が削減できます。
最終的には、ハイテク鋸にかえるだけで切断のコストが半減したなんて話もあります。
Wir erstellen Ihnen gerne eine Proberechnung, rufen Sie uns daher bitte an.
Vielen Dank, dass Sie bis zum Ende gelesen haben.
Sie können den Katalog über den untenstehenden Button kostenlos herunterladen.