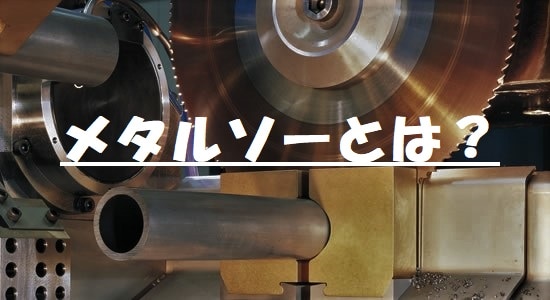
What is metal saw blade? Explanation of materials and blade types!
Table of contents [hidden]
- 1.Whatis metal saw blade?
- 2.About the material of metal saw blade
- 3.cutting with metal saw blade
- 4.Aboutthe blade type of metal saw blade
- 4.1.高低刃(HZ・C)
- 4.2.交互刃(チドリ・BW・面取り)
- 4.3.溝刃(ノッチ・CB・BN)
- 5.Regarding pitch selection
- 6.About SZ (depth of cut per tooth)
- 7.metal saw blade angle
- 8.Aboutcoating
- 8.1.鋸刃の耐摩耗性の向上
- 8.2.生産性の向上
- 8.3.費用と作業性の改善
What is metal saw blade?
メタルソーとは、切断するために金属で作られた円盤状の鋸です。
下記のように各部位に関して名称があります。
①ボア
切断機械と接続する穴部。径(大きさ)は機械メーカー、機種により異なります。
ボア径は、32h(ボア径32mm)、50 h(ボア径50mm)と表されます。
②ピンホール
切断機械と接続する際の補助となる穴部。
ピンホールの数、径(大きさ)は機械メーカー、機種により異なります。
③ハブ
切断機械と接続する際の、機械と接触する中心端面。
④有効径
切断できる範囲です。研磨するたびに、減少します。
⑤ピッチ
鋸刃の山と山の間の長さを表します。上記図の場合、ピッチ5mm P5と表します。
メタルソーを型式を表現する際は、
315Φ(外径)× 2.5t(厚さ)× 32h(ボア径)× P5(もしくは刃数)+ 刃型
などと表し、それぞれに意味があります。
>>Download the Daido Kogyo metal saw blade catalog
About the material of metal saw blade
メタルソーと呼ばれる高速度鋼(こうそくどこう、high-speed steel)は工具鋼における高温化での耐軟化性の低さを補い、より高速での金属材料の切削を可能にする工具の材料とするべく開発された鋼です。高速度工具鋼(high-speed tool steel)とも呼ばれます。
「ハイス」の呼称は、「ハイスピード・スチール」が縮まったもので、また、HSSと略記される高速度鋼は、高温化での硬さや耐軟化性を高めるべく、鋼にクロム、タングステン、モリブデン、バナジウムといった金属成分を多量に添加したもので焼入れ等の熱処理を施した後、研磨により成形して使用されています。
Compared to cemented carbide, it has inferior wear resistance but is superior in toughness and can be cut at higher speeds.Today, powder metallurgy is used to refine the structure and create even higher alloys.
「焼結高速度(工具)鋼」(粉末ハイス)や、物理気相蒸着(PVD)法による表面への窒化チタン(TiN)等の高耐摩耗性被膜の形成が盛んに行われており、これらを含めて超硬合金では靭性の不足する領域での金属加工に用いられる工具、主にはドリルやエンドミル、金属用鋸刃の材料として使われています。
また、コバルトを添加した高速度鋼はとくに「コバルト・ハイス」と呼ばれ、より焼きもどし抵抗性や高温硬さが高く、これは加工時により高温に曝されるステンレス鋼の穴あけなどに使用されます。
The Japanese Industrial Standards (JIS) specifies 13 types of high-speed steel as "JIS G4403." Among these, high-speed steel is identified by the symbol ``SKH'' preceding the number, which stands for Steel, Kougu (tool), and High-speed.
Excerpt from Wikipedia
Remember that metal saw blade are made of HSS (high speed steel) and cobalt high speed steel. In other countries, they are called M2 and M35.
About cutting with metal saw blade
The diagram below shows how the cutting edge of metal saw blade penetrates the material.
*Excerpt from Kinkelder materials
As can be seen from this figure, the cutting edge of the metal saw blade cuts into the material (cutting),
It is metal saw blade cutting to make chips and generate heat due to friction.
*The above process causes wear on the cutting edge metal saw blade.
>>Download the Daido Kogyo metal saw blade catalog
About the blade type of metal saw blade
We will introduce three typical blade types of metal saw blade.
高低刃(HZ・C)
It has been considered the basic blade shape for metal saw blade.
被切断材:ムク材や厚肉材向け
切削抵抗:小(2刃で切粉3分割)
面粗度:粗い ピッチ:4以上
備考:難削材に対応
交互刃(チドリ・BW・面取り)
薄肉パイプ等はこちらが基本となります。
Material to be cutting: For thin-walled pipes
Cutting resistance: Medium (2/3 of saw blade)
Surface roughness: Fine Pitch: 3-4
Note: For low speed/manual machines
溝刃(ノッチ・CB・BN)
The latest technology is here.
Materials to be cutting: thin-walled pipes, etc.
Cutting resistance: Large (one blade splits chips into two)
Surface roughness: Fine Pitch: 4-9
Remarks: For automatic machines. High speed rotation produces beautiful cutting surfaces.
*Requires mechanical rigidity and coating. Not suitable for angle cutting (can be used if angle cutting is not an issue)
この3つの刃型が基本となっておりますが、面粗度を重視で無垢材にも溝刃等を使っている実績もあり、上記以外の刃型(例えば不等ピッチ 等)の技術探求も盛んに行われております。
*The usage limits of metal saw blade and the criteria for determining whether something can be cut or not vary from user to user, so the basic principle is to ultimately determine the blade type specifically for the user after conducting actual cutting tests.
We will support you in establishing such judgment criteria.
About pitch selection
※大事なことは切断長を調べること※
切断長とは、刃物が材料に対して切り込んでいくときに一番長く切削する距離をいいます。
*From Kinkelder materials
The above diagram shows how our Kaltenbach cutting machine cuts a square pipe from bottom to top, and shows the part of the square pipe where cutting length (the longest distance that saw blade cuts into the material) is longest.
この1番刃に負荷がかかる切断長を基準に刃物のピッチ(刃数)を決定する必要があります。
Why is it necessary to select the pitch (number of teeth) according to cutting length?
仮に切断長に対して1つの刃が下から切り込みながら押し上げられ切削する場合、材料の切粉と熱が発生します。
その材料の切粉は負荷となり、刃に対して摩耗をあたえ鋸刃の消耗を左右します。
また、切断長全体を刃物が切り込みながら進むので切粉も切断長の長さで発生することになります。
その切粉がくるくるバネのように巻かれて刃底と呼ばれる部分に巻き取られていきます。
As you may have guessed, a pitch that is small for a long cutting length will clog (chips will accumulate at the bottom of the blade), and conversely, a large pitch for a short cutting length will not improve cutting efficiency.
In addition, the amount of cutting chips also changes depending on the SZ value, so this must also be taken into consideration. Therefore, it is necessary to select the appropriate pitch depending on the item being cut, the machine and saw blade.
For example, in our company based on the above Pitch Selection Process As an example, the load on the blade (denoted as SZ = depth of cut per blade) depends on the material to be cutting cut and the machine to be cutting cut, but if we assume a Kinkelder high technology saw blade with high rigidity Fully automatic cutting machine machine (cutting speed 150m/min), we calculate a load of SZ = 0.08mm depth of cut per blade, In a 50 square 2.3t pipe, the pitch is 10 can be calculated as follows.
※計算の詳細は紙面の関係で割愛いたします。切断する機械の周速により、ピッチの考え方も変わりますので弊社にてサポート致します。
About SZ (depth of cut per tooth)
※使っている機械によって違います。
切り込み量とは1刃あたりにどれだけ切削をさせるかということであり、これは、刃袋(刃底)と切断長と相関関係(俗にいう目詰まり)にあるといえます。
It is also affected by the rigidity of the cutting machine, and manual machines are set to small values, while high rigidity machines are set to high values. In addition, the thickness of saw blade and the side shape of saw blade (POWER shape) may also affect the setting.
基本的には摩耗の観点からも手動機等の切断時の切り上げが人力等の場合は最小で0.03mm、カルテンバッハ切断機等で比較的低速で油圧送りにて重切削をする場合は0.13mmぐらいまで設定することもあります。
また、切断する材料によりSZの考え方を変える必要もあります。
(非鉄=高く バネ鋼=低く)。
About the angle of metal saw blade
*Changing this might change your cutting results.
γ:スクイ角度 形や材質により変化させる
鉄 基本:18度(キンケルダー社推奨) アルミ等:25度
※ 参考400~500N/m㎡ パイプ
It is advisable to consider where the blade enters the material on your machine. Each company has its own differences (approach angle, swing, straight ahead).
In general, the harder the cutting material, the smaller the angle (shear rather than cutting)* approaching tipped saw blade cutting (rigidity and torque are required).
α:逃げ角度 形や材質により変化させる
鉄 基本:8度(キンケルダー社推奨) アルミ:12度
※ 参考400~500N/m㎡ パイプ
It is advisable to consider the position where the blade enters the material on your machine. Each manufacturer has their own differences (entrance angle, swing, straight movement).
Generally, the harder the material being cutting, the smaller the angle should be.
From the above, it can be said that the sharper the blade is, the easier it will dig into it and the more likely it will chip, and the thicker it will be, the stronger it will be, but the harder it will be to cut.
>>Download the Daido Kogyo metal saw blade catalog
コーティングについて
These days, there are black cutters and gold cutters, right?
There are three purposes for why coating is applied.
鋸刃の耐摩耗性の向上
① Improved surface hardness by coating (1,500 to 3,500 HV)
As a reference hardness
HSS: 760-840HV TCT (tungsten carbide): about 1400HV
② Smooth the surface and reduce frictional resistance on the cutting edge and overall surface
3) Reduction of heat damage to the saw board during cutting
④鋸刃表面の酸化防止
生産性の向上
(1) Can do cutting quickly → Can do cutting speed quickly. Can increase the amount of infeed.
②刃先の摩耗低減によるロングライフ化
③バリの発生低減
④ Cutting oil, etc. can be reduced
費用と作業性の改善
① Increased production volume per hour
②Reducing the burden on machines
③Reduction of consumable costs due to longer life (especially reduction in number of polishing times)
④Improvement of deburring work by reducing burrs
⑤Reduction of saw blade replacement time, etc.
⑥切削油を少なくできることによる消耗費軽減や作業環境の改善
コーティングの鋸刃は値段も高いですが、その分ライフが伸びれば特に再研磨するメタルソーは 研磨回数分 ✖ 伸びた本数分 の費用が削減できます。
最終的には、ハイテク鋸にかえるだけで切断のコストが半減したなんて話もあります。
We will give you a trial calculation, so please give us a call.
Thank you for reading to the end.
You can download the catalog for free using the button below.